Yes, there are more efficient solutions than traditional stud welding machines, depending on the specific application and requirements. Some of these alternatives offer faster welding times, improved energy efficiency, better precision, or reduced operational costs. Below are some advanced technologies and methods that can serve as alternatives to traditional stud welding:
Capacitor Discharge (CD) Stud Welding
How it works : CD stud welding uses capacitors to store electrical energy, which is then discharged in a very short burst to weld the stud to the workpiece.
Advantages :
Extremely fast welding process (milliseconds).
Minimal heat-affected zone (HAZ), reducing distortion and preserving material properties.
Suitable for thin materials and applications requiring high precision.
Applications : Ideal for thinner gauge materials like sheet metal, automotive panels, and electronics.
Drawn Arc Stud Welding with Advanced Controls
How it works : This method involves creating an arc between the stud and the workpiece, melting the surfaces before the stud is plunged into the molten pool.
Advantages :
Can handle larger studs and thicker materials.
Modern machines come with advanced controls, such as digital interfaces, automatic parameter adjustment, and real-time monitoring, improving efficiency and consistency.
Improved weld quality with less spatter and better fusion.
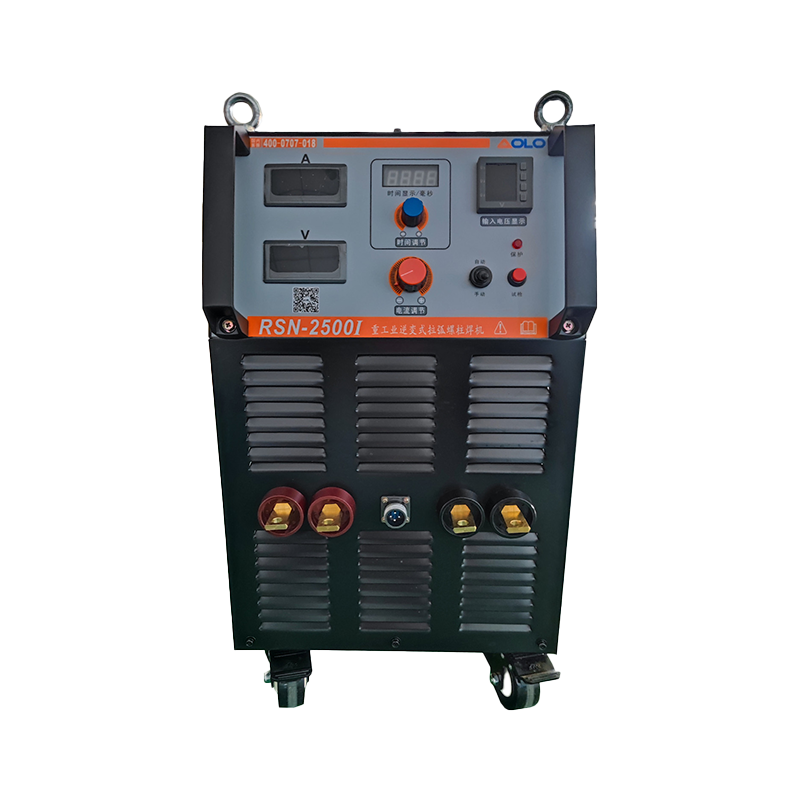
Applications : Construction, shipbuilding, and heavy manufacturing where larger studs are required.
Laser Stud Welding
How it works : Laser welding uses a high-energy laser beam to melt the stud and the base material, creating a strong bond.
Advantages :
Very precise and clean welds with minimal thermal distortion.
High-speed welding, especially for small studs.
No need for additional filler materials or flux.
Reduced post-weld cleanup.
Applications : Aerospace, medical devices, and other industries requiring high precision and clean finishes.
Friction Stir Welding (FSW)
How it works : FSW uses a rotating tool to generate frictional heat, softening the material and allowing it to be joined without melting.
Advantages :
No consumables (no studs required).
Low heat input, reducing distortion and improving joint strength.
Environmentally friendly, as it doesn’t produce fumes or spatter.
Applications : Automotive, aerospace, and railway industries for joining aluminum and other lightweight materials.
Resistance Projection Welding
How it works : In this method, the stud has small projections that concentrate the current and heat during welding, allowing for a strong bond.
Advantages :
Faster cycle times compared to traditional stud welding.
Can join multiple points simultaneously.
Minimal surface preparation required.
Applications : Automotive industry, particularly for attaching brackets, clips, and other small components.
Ultrasonic Metal Welding
How it works : Ultrasonic welding uses high-frequency vibrations to create friction between the stud and the workpiece, generating heat and forming a solid-state bond.
Advantages :
No melting required, preserving material properties.
Very fast and energy-efficient.
Clean process with no sparks, fumes, or filler materials.
Applications : Electronics, battery assembly, and other applications involving thin metals or dissimilar materials.
By evaluating these advanced technologies, you can find a solution that improves efficiency, reduces costs, and enhances the quality of your welding operations compared to traditional stud welding machines.
Contact Us