Submerged Arc Welding is a widely used welding process known for its high efficiency and excellent welding quality. Here are the key advantages of submerged arc welding machines that contribute to these benefits:
One of the most significant advantages of SAW is its ability to achieve high welding speeds. The submerged arc process allows for a larger weld pool and thicker layers of deposited metal, which translates to faster travel speeds compared to other welding methods. This efficiency is particularly beneficial in large-scale manufacturing environments where productivity is crucial.
SAW provides deep penetration into the base material, which is essential for creating strong, durable welds. The welding arc is submerged under a layer of granular flux, which helps maintain a consistent and stable arc. This characteristic enables the welder to penetrate deeper without the risk of burn-through, making it suitable for welding thick materials.
The use of a protective flux in SAW reduces oxidation and contamination during the welding process. This results in a cleaner weld with fewer defects, such as porosity or slag inclusions. The consistent arc stability and control over the welding parameters lead to uniform welds, which are critical for structural integrity.
SAW typically results in a smaller heat-affected zone compared to other welding processes. This is important because a smaller HAZ reduces the risk of warping or weakening the base material. The controlled heat input helps preserve the mechanical properties of the surrounding material, which is particularly important in applications where structural integrity is vital.
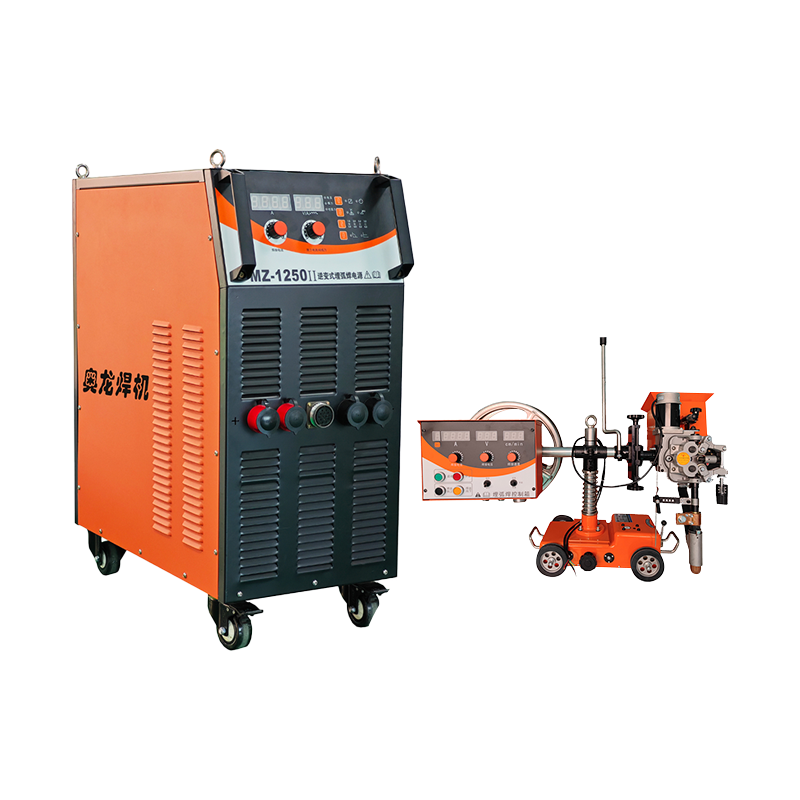
Since the arc is submerged under flux, SAW produces significantly less welding fume and harmful UV radiation compared to traditional arc welding methods. This not only improves the working environment for welders but also reduces the need for extensive ventilation systems, contributing to overall operational efficiency.
SAW machines can achieve high deposition rates, allowing for a larger amount of filler material to be added in a shorter time. This efficiency is beneficial for large projects, such as shipbuilding and construction, where speed is essential without compromising the quality of the weld.
Many submerged arc welding machines are designed for automation, enabling continuous welding operations. Automated SAW systems can be programmed for various welding tasks, leading to consistent results and further improving efficiency. Automation also reduces the risk of human error, enhancing overall welding quality.
SAW is versatile and can be used for various welding applications, including steel plates, pipes, and structural components. Its ability to weld different thicknesses and types of materials makes it suitable for industries such as shipbuilding, construction, and pressure vessel manufacturing.
The high-quality welds produced by submerged arc welding often require less post-weld treatment or finishing. This can save time and labor costs associated with additional grinding, cleaning, or repairing, contributing to the overall efficiency of the welding process.
The combination of high efficiency and good welding quality makes submerged arc welding a cost-effective choice for many industrial applications. The lower labor costs associated with automated processes, coupled with reduced material waste and fewer defects, can lead to significant savings in large-scale operations.
Submerged arc welding machines offer numerous advantages that enhance both efficiency and weld quality. From high welding speeds and deep penetration to consistent results and reduced environmental impact, SAW stands out as a preferred method in various industries. As manufacturers continue to seek improved productivity and quality in welding processes, the benefits of submerged arc welding will likely remain significant, reinforcing its role in modern fabrication and construction.
Contact Us