Ensuring the stability of an Argon Arc Welding Machine in adverse environments, such as high temperature and high humidity, requires addressing both the electrical and mechanical performance aspects, as well as considering the operational conditions.
Ensure that the machine's external casing is made from corrosion-resistant materials like stainless steel or coated aluminum. This will protect internal components from moisture-induced corrosion and physical damage due to high humidity.
Key components, such as power circuits and wiring, should be sealed with waterproof coatings or housed in moisture-resistant enclosures to prevent short circuits and corrosion.
To handle high temperatures, the internal components (especially power supplies and transformers) must be equipped with proper thermal insulation to prevent overheating.
Heat-resistant materials should be used for key components like cables and insulation on wiring to ensure that they perform optimally under high heat conditions.
High humidity and heat can cause overheating and excessive wear on electrical components. Integrating active cooling systems, such as fans or liquid cooling setups, will help maintain optimal operating temperatures and prevent overheating.
A smart temperature control system can adjust the machine's cooling speed based on real-time temperature data, ensuring that the machine does not overheat during prolonged welding sessions.
Ensure the welding machine has radiators or heat sinks to facilitate better heat dissipation and maintain the internal components at safe operating temperatures. This is especially crucial in high ambient temperatures.
Desiccants and moisture barriers: Incorporating desiccants (such as silica gel) or using moisture barriers inside the machine can help absorb any moisture buildup and reduce the risk of short-circuits and rust.
High humidity can often coincide with the presence of dust or water vapor particles, which could damage sensitive components. Ensure that the welding machine is sealed to prevent foreign particles from entering the electrical components, and if necessary, include air filters in the ventilation system to keep the interior free from dust.
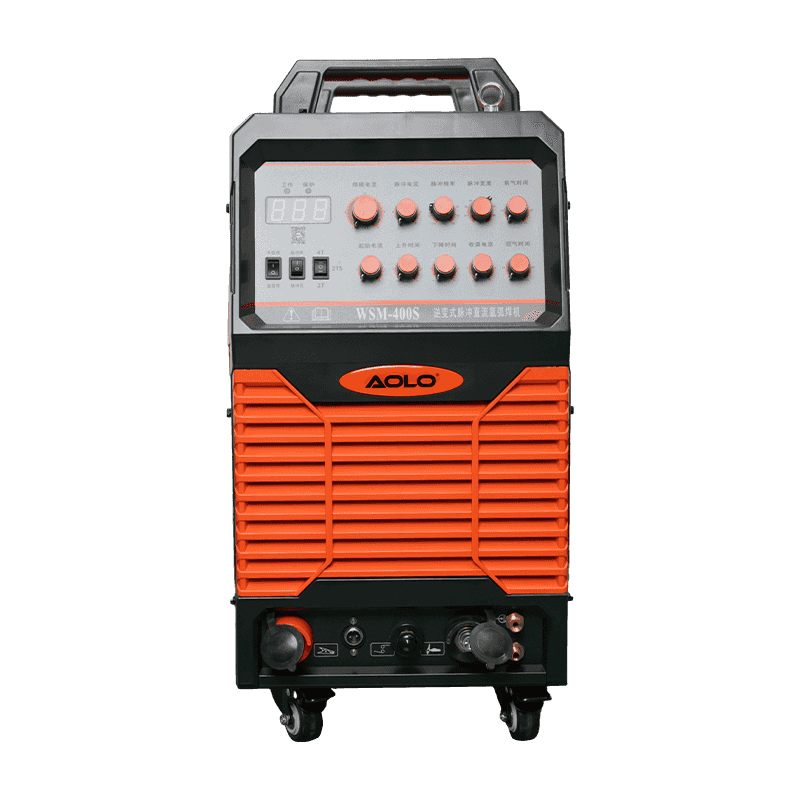
High temperatures and humidity can lead to fluctuations in power supply and the quality of the electrical current. Implement voltage stabilizers or surge protectors to ensure that the welding machine receives stable power. This prevents erratic behavior or damage to sensitive electronics due to unstable input.
Use high-quality insulated cables and connectors that are rated for operation in high-humidity environments. These should be IP-rated (Ingress Protection) to prevent moisture from seeping into the internal wiring and connections.
Integrate sensors within the welding machine to monitor the ambient temperature and humidity levels. The machine can then adjust its cooling or power output accordingly, and provide operators with alerts if the environmental conditions become detrimental.
A diagnostic system can continuously track machine performance and alert operators to issues such as excessive heat or moisture buildup. This system would help detect early signs of instability and allow preventive measures to be taken before severe damage occurs.
Adaptive control technology can be used to adjust welding parameters in real-time based on temperature and humidity conditions. This includes adjusting the arc length, welding speed, and electrode feed to compensate for environmental factors.
For certain materials, preheating the workpiece can help avoid problems related to high humidity. In cases of extreme humidity, drying the electrodes and filler materials before use can prevent issues such as porosity in the weld bead.
Routine checks should be conducted on key components like the cooling system, power supply, and seals. This ensures that moisture and heat buildup do not negatively affect the machine's performance.
Welding cables and hoses should also be checked periodically to ensure they remain intact and are not degraded by high heat or humidity.
Regularly calibrate the machine’s control systems to ensure that it continues to function optimally, even under fluctuating environmental conditions. This includes checking the voltage settings and welding parameters.
To ensure the stability of an Argon Arc Welding Machine in adverse environments like high temperature and high humidity, it is crucial to integrate advanced design features that protect against environmental factors, enhance cooling systems, and incorporate smart technologies for monitoring and adaptive control. Additionally, using high-quality, moisture-resistant materials and providing regular maintenance will ensure long-term reliability and performance.
Contact Us