One of the major advantages of Argon arc welding machines is the stable electric arc they provide. The use of argon gas as a shielding gas prevents contamination of the weld pool by air, especially oxygen and nitrogen, which ensures a clean and stable arc. This stability allows for very fine control over the heat input into the workpiece, which is crucial in applications where precision is critical.
The inert nature of argon prevents unwanted reactions with the molten weld pool, helping maintain a consistent and smooth arc.The precision with which heat is applied ensures that the welding process does not damage thin or delicate materials, reducing the risk of overheating, warping, or burning through.
Argon arc welding allows for precise control over the weld pool and the depth of penetration. This is especially important when welding thin materials or when a high-quality surface finish is required. The operator can make fine adjustments to the welding current and speed, ensuring an even weld bead and controlling the penetration depth with accuracy.
Depending on the settings, it is possible to create both shallow and deep welds with consistent results.The precise control over heat input ensures that the weld bead is smooth, even, and uniform, without the defects typically associated with other welding methods, such as spattering or undercutting.
Argon arc welding is particularly advantageous when working with thin-walled materials such as stainless steel, aluminum, and titanium. The ability to precisely control the heat input allows for welding on materials with thicknesses as low as 0.5 mm or less, without burning through or distorting the base material.
Thin materials are particularly susceptible to heat distortion, but Argon arc welding's low heat input minimizes this risk.When welding thin materials, the welder can produce narrow and clean weld beads, avoiding excessive buildup that would weaken the joint.
Argon arc welding offers high precision not only for flat welds but also for out-of-position welding (such as vertical, overhead, or horizontal positions). The stable arc and low spatter make it easier to control the welding process, even when working in challenging positions.
The ability to weld in various positions with stability ensures that Argon arc welding is ideal for components where access is limited.
Less spatter: Compared to other welding techniques, Argon arc welding produces minimal spatter, which helps maintain better control and consistency in difficult positions.
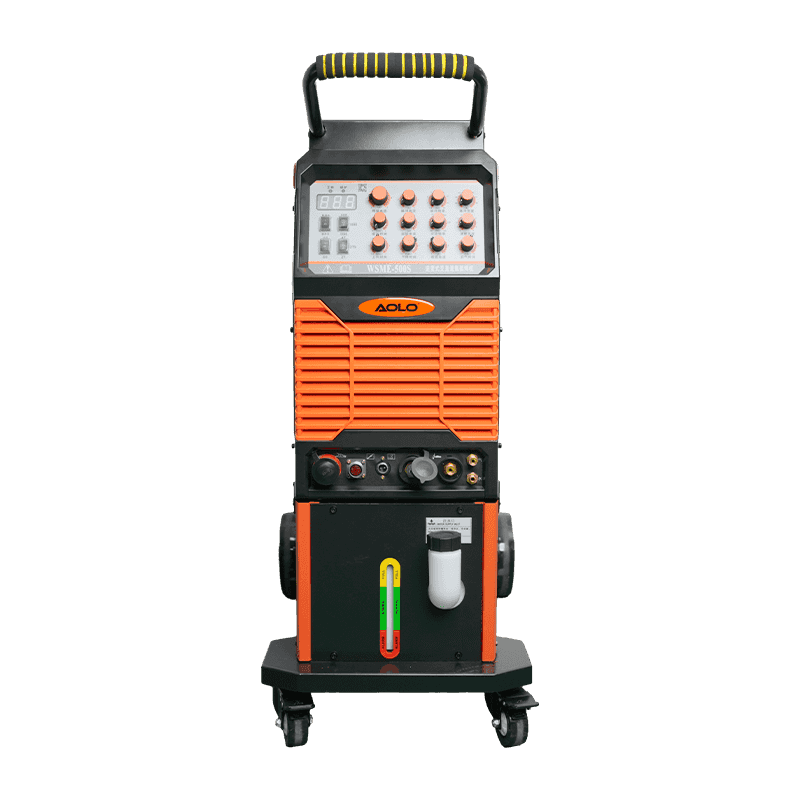
Modern Argon arc welding machines often feature pulsed TIG capabilities, which further enhance control over the welding process. By varying the current between a low and high setting in pulses, this technique allows the welder to fine-tune the heat input, enabling better control over weld bead formation, particularly when welding heat-sensitive materials.
Pulsed arc welding minimizes overheating while allowing higher energy input when necessary.The pulsing feature helps in controlling heat distribution, reducing distortion, and providing better control over thin or high-precision components.
The precision offered by Argon arc welding results in welds with excellent surface finish and mechanical properties. Unlike other methods like MIG or stick welding, which can result in more spatter and less control, Argon arc welding typically results in cleaner, higher-quality welds.
The tight control over the arc prevents defects such as porosity, cracking, and inconsistent penetration.The consistent heat control results in smooth, visually appealing welds that are ideal for applications where appearance matters (e.g., in the aerospace or medical industries).
The precise control over heat input not only prevents damage to thin materials but also reduces distortion in thicker components. This is important in industries where the alignment and geometric accuracy of the welded parts are critical, such as in aerospace or automotive applications.
Precise heat control reduces the likelihood of warping or distortion, ensuring that parts remain in proper alignment.The welder can ensure that weld joints are created with minimal stress or deformation, especially important in applications that demand tight tolerances.
Argon arc welding can be used for a wide range of metals, including stainless steel, aluminum, magnesium alloys, and copper. Its precision and control over heat make it suitable for both ferrous and non-ferrous materials, ensuring that weld quality remains high across different applications.
Whether in aerospace, automotive, or precision manufacturing, Argon arc welding offers a level of control and weld quality that is difficult to match with other welding processes.
Contact Us