Submerged Arc Welding Machine has a series of unique advantages and features compared to other welding equipment, making it particularly good in some special welding applications. The following are the advantages and features of submerged arc welding machine compared with other welding equipment (such as manual arc welding, TIG welding, MIG/MAG welding, etc.):
Submerged arc welding is an automated welding process, and the welding speed is usually faster, which can significantly improve production efficiency. Compared with welding methods such as manual arc welding (SMAW), submerged arc welding has a faster welding speed and is particularly suitable for large-scale batch production. The reasons for the fast welding speed are:
The arc is completely covered by the protective slag, avoiding exposure to the outside air, making the welding process more stable and greatly improving production efficiency.
The automatic wire feeding system can continuously supply welding wire, so that the welding process does not require frequent replacement of welding rods.
Since the welding area is completely covered by slag, submerged arc welding can effectively prevent problems such as oxidation and nitridation, and the purity and strength of the welded metal are guaranteed. Compared with manual metal arc welding (SMAW), the quality of submerged arc welding welds is generally more consistent, with no electrode residue and fewer welding defects (such as pores, cracks, etc.). The advantages of submerged arc welding are reflected in the following aspects:
Since the arc is in the slag, the melting temperature of the weld metal is uniform, avoiding irregular ripples on the weld surface.
The protective slag can isolate the air and avoid common welding defects such as pores and slag inclusions.
The welds of submerged arc welding have higher strength, hardness and corrosion resistance.
Compared with welding methods such as manual arc welding that require a high level of technology, submerged arc welding, as an automated welding process, requires relatively low technical level of operators. The welding process of the submerged arc welding machine requires almost no human intervention, and the equipment can automatically complete the welding under the set parameters. In this way, not only the production efficiency is improved, but also the welding defects caused by improper operation are reduced.
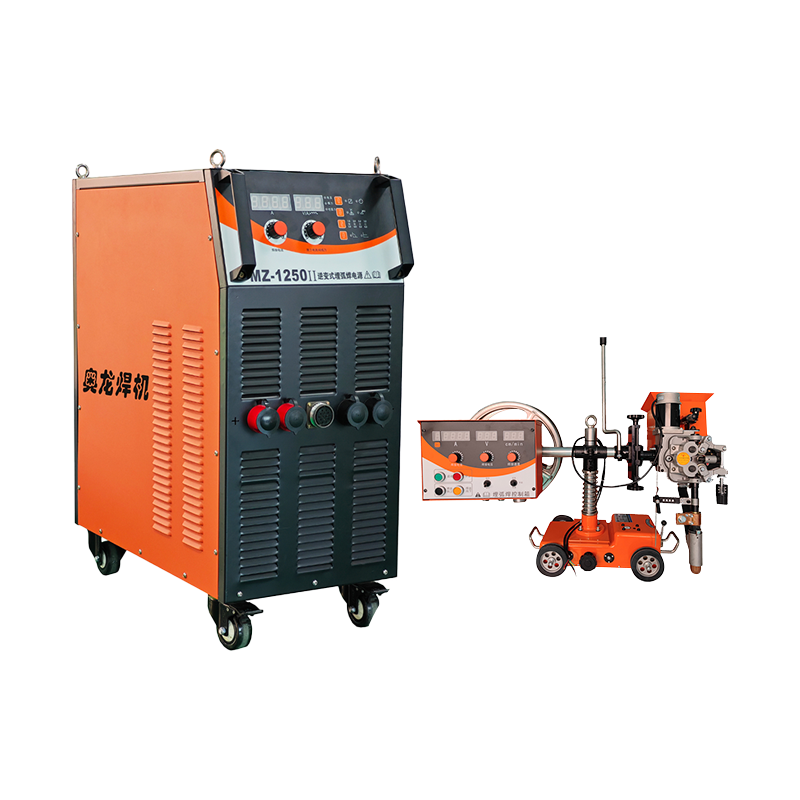
During the welding process of submerged arc welding, the welding arc is completely covered by slag, so less smoke and gas are generated, reducing pollution in the working environment. In addition, the noise of submerged arc welding is also lower. Compared with other methods such as manual arc welding, submerged arc welding is more suitable for use in environments that require low noise and low pollution.
Submerged arc welding is particularly suitable for welding thick plates and large structures. When welding thick metals, submerged arc welding machines can provide a large welding current, thereby obtaining a large molten pool and ensuring the stability and strength of the welding. This makes submerged arc welding widely used in some heavy machinery, shipbuilding, pressure vessels and other fields. Compared with other welding methods, the arc stability and high welding efficiency of submerged arc welding give it unique advantages in these applications.
Due to the high and concentrated arc temperature of submerged arc welding, the heat-affected zone during welding is relatively small, which can reduce welding deformation and stress, which is particularly important for some welding projects with high deformation requirements. Compared with manual arc welding, the heat input of submerged arc welding is more precise and can effectively control the welding quality, especially in the welding of thin plates and complex structures.
Because the submerged arc welding machine uses an automatic wire feeding system, the supply of welding wire can be more accurately controlled to avoid excessive waste. Moreover, submerged arc welding has a high efficiency and can reduce labor costs. In addition, due to the high welding quality, the need for post-weld repair is reduced, which further reduces costs.
Submerged arc welding can be operated in horizontal, vertical, crane and other multiple welding positions. Although special welding processes and technical support may be required in certain specific welding positions (such as vertical welding), submerged arc welding can be applied in more scenarios than other welding methods, especially in large structures and complex environments.
Submerged arc welding machines are very suitable for automated production lines and can be linked with manipulators, conveyor belts and other equipment to complete continuous welding tasks. This makes submerged arc welding an ideal choice for large-scale and batch production, and is widely used in occasions such as pipeline welding and steel structure welding that require large-scale production.
Submerged arc welding machines have good adaptability to different types of materials, alloys and thicknesses. By adjusting the welding parameters, submerged arc welding can adapt to the welding requirements of a variety of welding materials (such as carbon steel, alloy steel, stainless steel, etc.). It can also adapt to higher operating temperatures and complex welding environments.
Compared with other welding equipment, submerged arc welding machines have obvious advantages in efficiency, welding quality, degree of automation and scope of application. It can ensure welding quality while welding efficiently, and is suitable for welding tasks in thick plates, large structures and mass production. However, submerged arc welding also has its limitations. For example, for small workpieces or welding tasks that require fine control, other welding methods such as TIG welding or MIG welding may be more suitable. Choosing the right welding equipment needs to be determined according to specific welding needs and application environment.
Contact Us